What are the uses of blow molding equipment?
The blow molding equipment used includes plasticating extruders, blow molding heads, blow molding equipment, gas supply assembly, and cooling assembly. High rigidity, high speed, large power of the spindle system, small inertia of the feed system, excellent function, super-precise, high-speed and high-performance of the CNC machine (cnc) system, the machine bed function is unchanged, and the tool clamping system is safe. Reliable is the primary feature of modern high-speed cutting machine tools? l8’9-year-old mold: box-type cooling, milling a groove behind the cavity, adding seals, using a small mold on the plate: cooling water channel, water cooling 2015 -1-10 5 Benefits: It is suitable for torsion blow molding without cutting the continuous production of the parison, blowing a small container connected with the neck and tail. For the non-neck blow molding products, the parison cutter can be installed inside the mold, which is more suitable for blowing. The container has a handle, and the handle itself blocks the products that are not in communication with the body. Projecting a wire to a circular torsion surface to obtain a space spiral guide; the end of the wire is at a reference plane perpendicular to the wire at the point; the end of the wire is made to have a diameter (p4m) Circle; the circle is scanned along the wire to obtain a spiral feature; (1) The spiral feature is rotated about the x axis by a transform about 30.
The design scheme firstly analyzed the geometry of the pet bottle and the blow molding process of the preform, the temperature control of the mold working department, etc.; then proposed the structure of the hollow blow molding equipment and explained its work.
Hollow blow molding machine
The design of the hollow blow molding machine gives all kinds of shapes of polyvinyl chloride transparent blow molding bottles. The operation of silk screen printing or modern printing technology makes the transparent transparent blow molding bottle more attractive color, which makes it a large amount. The land is flooding the market. Not confidential. In order to increase the competitiveness of the product, it is necessary to minimize the thickness of the container wall.
In the multi-layer co-extrusion blow molding equipment, due to the technical requirements of special products, the bottle wall can reach a seven-layer structure; for the special-shaped fuel tank for automobiles, the main body of the fuel tank is multi-layered for better impermeability. Structure, the fuel tank from the seams to the ridges, the structure of the layer. The draft angle is not required for the hollow blow molding, and it is shortened. Under normal circumstances, if the product profile has ripples, in order to facilitate the ejection from the mold, the draft angle should be designed. Although there are corrugations, the draft angle can be omitted because of the choice of the parting surface. Use sweep, loft or blend to create a tree surface, as shown in Figure 10sweep feature surface, adjust and optimize the feature mesh of the surface control point and surface, or use the slice method to approximate the surface to obtain a smooth feature surface. Compression molds are also used to mold certain extraordinary thermoplastics such as difficult-to-melt thermoplastics (such as polyvinyl fluoride) blanks (cold press molding), optically high resin lenses, and lightly foamed nitrocellulose vehicles. Destination disk, etc.
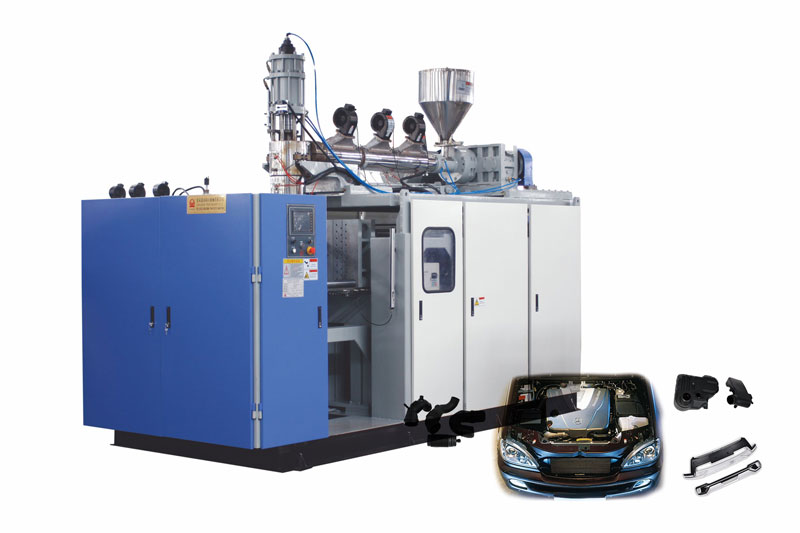
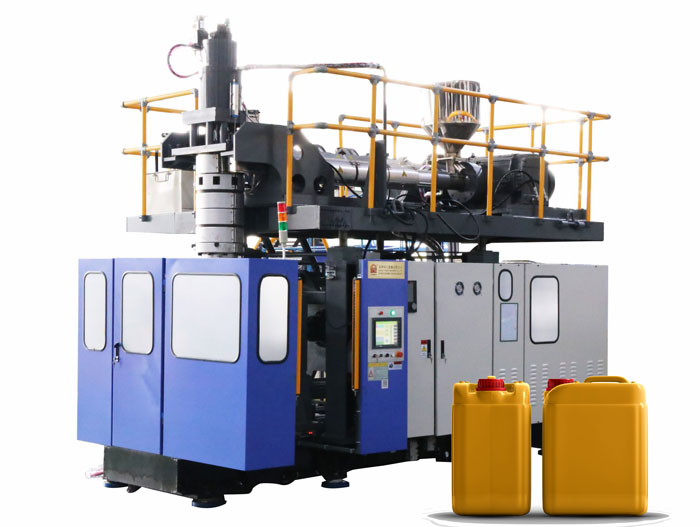