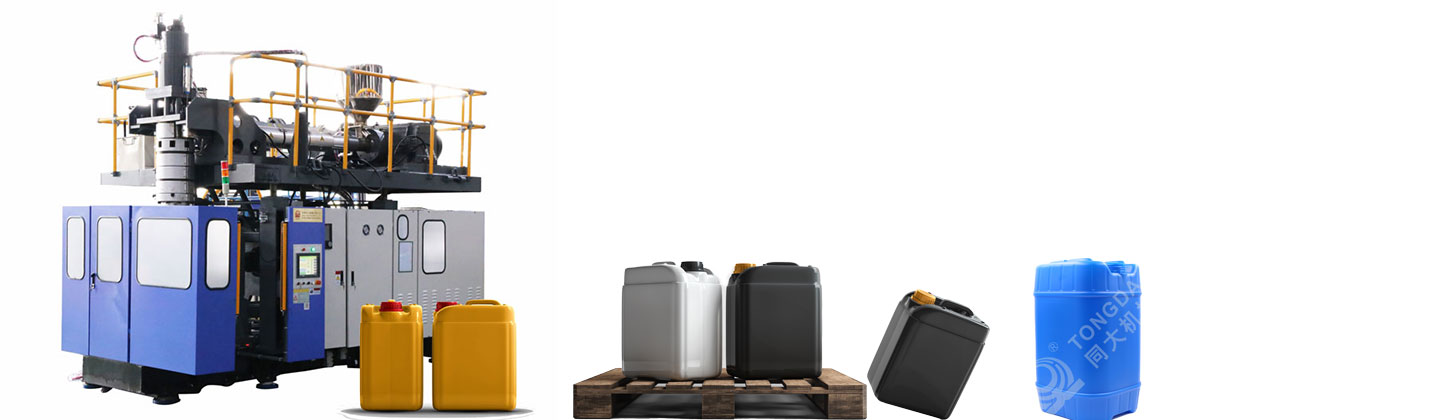
Stacking Barrel Blow Molding Machine
Table of Contents
- 1:Differences Between Stackable Barrels And Regular Plastic Barrels
- 2:Advantages Of Stacking Barrels
- 3:The Development Status Of Stacking Bucket Industry
- 4:Material Selection For Blow-Molded Plastic Stacking Buckets
- 5:Blow Molding Techniques For Plastic Stacking Buckets
- 6:Environmental Sustainability In Blow-Molded Plastic Stacking Bucket Production
- 7:Main Steps And Characteristics In Production Of Stacking Buckets
- 8:Quality Control In The Blow Molding Process Of Stacking Buckets
- 9:Key Considerations In Designing Blow Molding Molds For Stacking Buckets
- 10:Methods To Improve The Efficiency Of Blow Molding Process
Differences between stackable barrels and regular plastic barrels
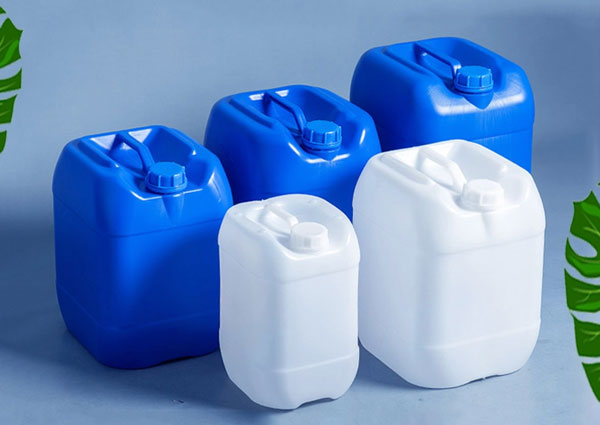
Structure and Design:
Stackable barrels typically consist of two parts (top and bottom) that can nest and stack, facilitating storage and transportation. Regular plastic barrels are usually designed as a single unit without the stacking functionality.
Durability:
Stackable barrels often use high-strength materials, offering better durability and the ability to withstand significant weight and impact. Regular plastic barrels have relatively lower durability and are generally suitable for light-load transportation and storage.
Usage Scope:
Stackable barrels are suitable for logistics, warehousing, transportation, etc., commonly used for storing and transporting powdered or granular items. Regular plastic barrels are more commonly used in household and daily life, such as storing food, liquids, etc.
Cost:
Stackable barrels typically require special design and manufacturing, resulting in higher costs. Regular plastic barrels have lower manufacturing costs and are relatively inexpensive.
Advantages of stacking barrels
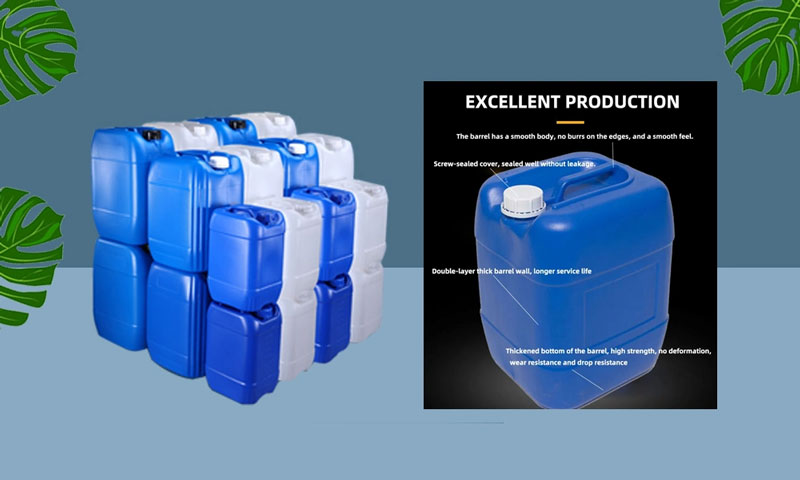
Stackable barrels have widespread applications in logistics, warehousing, and transportation, and the main reasons for choosing them include:
Excellent Stacking Effect:
The special structure and design of stackable barrels allow multiple barrels to nest and stack, saving storage space and improving accessibility. Compared to regular plastic barrels, stackable barrels exhibit superior stacking efficiency.
Strong Durability:
Stackable barrels are typically constructed with high-strength materials, capable of withstanding significant weight and impact. This durability meets the requirements for containers in logistics, warehousing, and transportation.
Convenient Operation:
The special design of stackable barrels makes loading and unloading operations more convenient and secure. Additionally, stackable barrels are relatively lightweight, making them easier to handle.
Environmentally Friendly and Energy-Efficient:
Stackable barrels are often made of plastic, a material with high environmental friendliness and recyclability compared to other materials. Moreover, the reusability of stackable barrels helps reduce waste generation.
Cost-Effective:
While the manufacturing cost of stackable barrels may be relatively high, their durability and reusability contribute to long-term cost reduction. Stackable barrels offer improved efficiency and economic benefits over extended periods of use.
The development status of stacking bucket industry

Market Demand:
The demand for stacking buckets is influenced by various sectors such as logistics, warehousing, agriculture, manufacturing, and more. An increase in these industries often corresponds to a higher demand for efficient storage and transportation solutions, including stacking buckets.
Material Innovations:
Innovations in materials, especially those that enhance durability, weight-bearing capacity, and environmental sustainability, can impact the stacking bucket industry. Manufacturers may explore new materials or adopt eco-friendly options to align with market trends.
Design and Technology:
Advances in design and manufacturing technologies contribute to the development of more efficient and user-friendly stacking buckets. Improved stacking mechanisms, safety features, and ergonomic designs can enhance the market competitiveness of stacking bucket products.
Regulatory Environment:
Changes in regulations related to materials, manufacturing processes, or environmental standards can affect the industry. Compliance with such regulations may influence the choice of materials and production methods within the stacking bucket sector.
Global Economic Trends:
The economic climate, both globally and regionally, plays a crucial role in the growth of various industries. Economic stability and growth often correlate with increased industrial activities, positively impacting the demand for stacking buckets.
Sustainability and Recycling:
Growing awareness of environmental issues and sustainability may drive the industry towards more eco-friendly practices. Manufacturers adopting recycling initiatives or producing reusable stacking buckets might gain a competitive edge.
Competition and Market Dynamics:
The competitive landscape within the stacking bucket industry, including the presence of key players and market dynamics, influences the overall development. Price competition, product differentiation, and strategic partnerships are factors that contribute to industry growth.
Material selection for blow-molded plastic stacking buckets
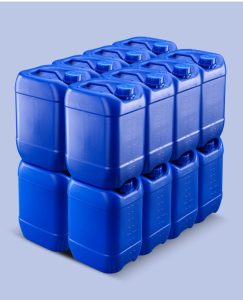
High-Density Polyethylene (HDPE):
Properties: Lightweight, rigid, excellent chemical resistance, impact resistance.
Applications: Commonly used for general-purpose stacking buckets due to its versatility and durability. Suitable for various industries, including agriculture, food processing, and manufacturing. Polypropylene (PP):
Properties: Lightweight, rigid, resistant to chemicals and moisture, good impact strength. Applications: Ideal for stacking buckets used in food and beverage industries, thanks to its suitability for contact with consumable goods. Also used in chemical and industrial applications.
Polyethylene Terephthalate (PET):
Properties: Transparent, lightweight, strong, recyclable. Applications: Often used for clear or transparent stacking buckets. Commonly found in the beverage industry for packaging and storage. Low-Density Polyethylene (LDPE):
Properties: Flexible, resistant to impact, excellent chemical resistance.
Applications: Suitable for applications where flexibility is important, such as in the storage of materials that may shift during transport.
Polyvinyl Chloride (PVC):
Properties: Durable, chemical-resistant, flame-retardant options available. Applications: Used in stacking buckets where fire resistance or specific chemical resistance is required, such as in certain industrial settings. Polycarbonate (PC):
Properties: High impact resistance, transparent, heat-resistant. Applications: Suitable for stacking buckets where clarity, impact resistance, and resistance to high temperatures are essential. Recycled Plastics:
Properties: Variable based on the source material. Applications: Increasingly, recycled plastics are being used in the production of stacking buckets to align with sustainability goals. The properties depend on the specific type and blend of recycled materials. Biodegradable Plastics:
Properties: Variable; designed to break down over time.
Applications: Used in environmentally conscious applications where biodegradability is a priority. However, considerations of performance and longevity are crucial.
UV-Resistant Plastics:
Properties: Enhanced resistance to ultraviolet (UV) radiation.
Applications: Suitable for outdoor applications where exposure to sunlight may cause degradation. UV-resistant plastics help maintain product integrity over extended periods. Material selection should consider factors such as the intended use, environmental conditions, regulatory compliance, and end-of-life considerations. Each material has its own set of advantages and limitations, and the choice depends on the specific requirements of the stacking bucket application.
Blow molding techniques for plastic stacking buckets
Blow molding is a manufacturing process used to produce hollow plastic parts, and it can be adapted to create plastic stacking buckets with various shapes, sizes, and features. Here are the primary blow molding techniques employed in the production of plastic stacking buckets:
Extrusion Blow Molding:
Process Overview: In extrusion blow molding, a molten tube (parison) of plastic is extruded through a die and captured in a mold cavity. Compressed air is then introduced into the parison, forcing it to conform to the shape of the mold.
Applications: Widely used for producing simple to moderately complex shapes, such as cylindrical or tapered stacking buckets. It is suitable for high-volume production.
Injection Blow Molding:
Process Overview: Injection blow molding combines elements of injection molding and blow molding. A preform is first injection molded, and then it is transferred to a blow mold where it is inflated to the desired shape.
Applications: Suitable for producing complex shapes with tight tolerances. Commonly used for small to medium-sized stacking buckets with intricate designs.
Stretch Blow Molding:
Process Overview: In stretch blow molding, a preform is first injection molded. The preform is then heated and stretched in both axial and radial directions before being blown into the final shape using compressed air.
Applications: Ideal for producing lightweight and high-clarity containers, such as PET stacking buckets commonly used in the beverage industry.
Continuous Extrusion Blow Molding:
Process Overview: Continuous extrusion blow molding involves a continuous extrusion of a parison, which is shaped and molded as it is continuously extruded. The molded part is then cut to the desired length.
Applications: Suitable for producing long, continuous shapes. Can be used for applications where a seamless appearance is desired.
Coextrusion Blow Molding:
Process Overview: Coextrusion blow molding involves using multiple layers of plastic materials in the parison. This allows for the creation of stacking buckets with layers of different properties, such as enhanced strength or barrier properties.
Applications: Useful when different properties are required in different parts of the stacking bucket, such as enhanced UV resistance on the outer layer.
Rotational Blow Molding:
Process Overview: Rotational blow molding, or rotomolding, involves rotating a mold in an oven while the plastic material melts and coats the interior. The mold is then cooled, and the part is removed.
Applications: Suitable for large and complex stacking buckets, often used for industrial and heavy-duty applications.
Choosing the appropriate blow molding technique depends on factors such as the desired bucket design, material selection, production volume, and cost considerations. Manufacturers often select the technique that best suits the specific requirements of the stacking bucket application.
Environmental sustainability in blow-molded plastic stacking bucket production:
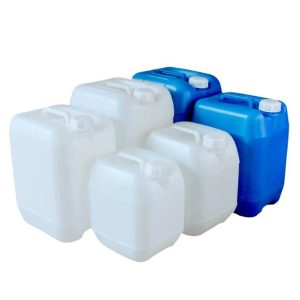
Environmental sustainability is a critical aspect of modern manufacturing, and the production of blow-molded plastic stacking buckets is no exception. Here are key considerations and practices related to sustainability in this manufacturing process:
Material Selection:
Recycled Content: Opt for materials with recycled content to reduce the demand for virgin plastics. Using recycled materials in blow molding helps mitigate the environmental impact of plastic production.
Biodegradable Options: Explore biodegradable plastics or bio-based materials that break down more easily, contributing to a reduction in long-term environmental impact.
Energy Efficiency:
Process Optimization: Implement energy-efficient practices in the blow molding process. This includes optimizing heating and cooling cycles, utilizing advanced machinery, and adopting technologies that minimize energy consumption.
Renewable Energy Sources: Consider sourcing energy from renewable sources to power blow molding operations, reducing the carbon footprint associated with energy consumption.
Waste Reduction:
Closed-Loop Systems: Implement closed-loop recycling systems within the manufacturing facility to recycle and reuse process waste. This can include reusing excess plastic material and recycling defective or scrap products.
Material Efficiency: Optimize material usage to minimize waste during the blow molding process. This involves efficient design practices and the use of technologies that reduce material wastage.
Packaging and Transportation:
Lightweight Design: Design stacking buckets with a focus on lightweight construction while maintaining structural integrity. Lightweight products contribute to reduced material usage and lower transportation-related emissions.
Eco-Friendly Packaging: Explore sustainable packaging options for the transportation of stacking buckets. This may include using recyclable materials or adopting packaging designs that minimize environmental impact.
End-of-Life Considerations:
Recyclability: Design stacking buckets with recyclability in mind. Clearly label products with recycling symbols, and work towards ensuring that the materials used are easily recyclable in existing waste management systems.
Product Lifecycle Analysis: Conduct a lifecycle analysis of the product to understand its environmental impact from production to disposal. Use this information to make informed decisions on improving sustainability throughout the product’s life.
Regulatory Compliance:
Adherence to Standards: Ensure compliance with environmental standards and regulations governing plastic production. Stay informed about evolving regulations related to plastics and environmental impact, and adjust practices accordingly.
Collaboration and Certification:
Industry Collaboration: Collaborate with industry organizations and stakeholders to share best practices, innovations, and technologies related to sustainable plastic production.
Certifications: Seek certifications such as ISO 14001 (Environmental Management System) to demonstrate a commitment to environmental responsibility and compliance with international standards.
Consumer Education:
Product Disposal Guidance: Provide clear information to consumers on how to responsibly dispose of or recycle plastic stacking buckets. Educate consumers on the environmental impact of different disposal methods.
By integrating these sustainability considerations into blow-molded plastic stacking bucket production, manufacturers can contribute to reducing the environmental footprint of their operations and products.
Main steps and characteristics in production of stacking buckets
The blow molding technique plays a crucial role in the manufacturing process of stacking buckets. Here are the main steps and characteristics of its application:
Mold Design:
Develop a specific mold design for blow molding stacking buckets, ensuring that the mold shape meets the requirements of the final product.
Consider the dimensions, structure, and stacking characteristics of stacking buckets, designing the mold to achieve consistency and production efficiency.
Material Selection:
Choose plastic materials suitable for blow molding, typically polyethylene (PE) or polypropylene (PP).
Select plastic materials with sufficient strength, wear resistance, and stacking stability based on the purpose and characteristics of stacking buckets.
Extrusion and Preform:
Extrude the chosen plastic material through an extrusion machine to form a tubular preform, known as “blow molding parison” or “blow molding preform.”
Design the extrusion machine’s die head to match the shape of stacking buckets, ensuring that the preform material meets the design requirements.
Blow Molding:
Place the preformed plastic material into the blow molding mold and initiate the blow molding machine.
Inflate the preformed parison by injecting high-pressure air, gradually filling the mold cavity and obtaining the mold’s shape.
Cooling and Solidification:
After blow molding is complete, rapidly cool and solidify the plastic through a cooling system, ensuring that the stacking buckets maintain the required shape and structure.
Control the cooling process to avoid internal stress and deformation.
Trimming and Post-Processing:
Trim and remove excess plastic from the blow-molded stacking buckets.
Perform necessary post-processing tasks, such as attaching labels, spraying, or printing.
Quality Control:
Implement rigorous quality control measures, inspecting the dimensions, shape, and surface quality of stacking buckets.
Use modern inspection equipment, such as image recognition systems, to ensure that each product meets specifications.
Packaging and Distribution:
Package the blow-molded stacking buckets to ensure they remain undamaged during transportation and storage.
Use eco-friendly packaging materials in line with sustainable development principles.
Sustainable Practices:
Consider using recyclable materials to promote sustainable production of stacking buckets.
Seek to reduce waste, improve energy efficiency, and implement environmentally friendly practices to make the blow molding manufacturing process more sustainable.
The blow molding technique effectively transforms molten plastic material into stacking buckets with specific shapes and functions, providing an efficient, precise, and controllable production process for stacking bucket manufacturing.
Quality control in the blow molding process of stacking buckets
Quality control in the blow molding process of stacking buckets is a crucial step to ensure that the final products meet specifications and customer requirements. Here are some quality control measures that may be implemented throughout the manufacturing process:
Mold Inspection:
Conduct a detailed inspection of the blow molding molds before use to ensure their design aligns with product specifications.
Regularly maintain and clean molds to prevent dirt or damage that could affect product quality.
Raw Material Quality Control:
Conduct rigorous quality checks on the plastic raw materials used to ensure they meet product requirements.
Employ proper storage and handling practices for raw materials to prevent impurities and contamination.
Extrusion and Preforming Control:
Monitor the operation of the extrusion machine to ensure even extrusion of the preforming material.
Use an automated control system to adjust extrusion machine parameters to maintain stable production.
Blow Molding Process Monitoring:
Real-time monitoring of key parameters such as temperature, pressure, and extrusion speed during the blow molding process.
Equip sensors and monitoring systems to promptly detect production anomalies and take corrective measures.
Cooling and Solidification Control:
Control the cooling system to ensure thorough cooling and solidification of plastic within specified timeframes.
Use appropriate cooling times and temperatures to prevent internal stress and deformation.
Trimming and Post-Processing Inspection:
Inspect trimming and post-processing tasks to ensure the processed products meet specifications.
Utilize automation equipment or visual inspection systems to enhance the consistency and precision of trimming and post-processing.
Final Product Inspection:
Perform a comprehensive inspection of blow-molded stacking buckets, including dimensions, shape, and surface quality.
Conduct sampling inspections or 100% inspections to ensure each product meets quality standards.
Packaging Inspection:
Inspect the packaging process to ensure that blow-molded buckets remain undamaged during packaging.
Ensure the use of environmentally friendly packaging materials to prevent external factors from affecting the products.
Recording and Traceability:
Record key parameters and inspection results at each production stage.
Implement a traceability system capable of tracing each product back to its production batch and raw material information.
By implementing stringent quality control measures, the blow molding process for stacking buckets can consistently maintain a high level of quality throughout the entire production process.
Key considerations in designing blow molding molds for stacking buckets
Product Design Requirements:
Determine the design specifications for stacking buckets, including dimensions, shape, and wall thickness.
Consider the stacking performance and structural characteristics of stacking buckets to ensure the mold design meets functional requirements.
Mold Structure Design:
Design the mold structure to accommodate preforming materials and accurately shape the product during the blow molding process.
Consider mold opening and closing mechanisms, mold cavity layouts, cooling systems, etc., for efficient production.
Cooling System Design:
Optimize the design of the cooling system to ensure even cooling of plastic materials within the mold, avoiding internal stress and defects.
Use cooling channels and nozzles to improve cooling efficiency and ensure product quality and stability.
Parting Line and Venting System:
Set appropriate parting lines for easy demolding after shaping.
Design an effective venting system to ensure smooth air evacuation, preventing bubbles and defects in the mold.
Mold Actuation Method:
Choose the appropriate mold actuation method, such as manual, automatic, or pneumatic actuation, to enhance production efficiency.
Ensure smooth mold opening and closing actions, reducing wear on the mold and mechanical equipment.
Surface Treatment and Coating:
Treat the mold surface appropriately and apply coatings to improve mold wear resistance and prolong its service life.
Select suitable coating materials to prevent plastic adhesion and reduce surface defects on the product.
Maintenance of the Mold:
Consider the mold’s ease of maintenance, ensuring convenient and fast cleaning, replacement, and repairs.
Implement a regular maintenance plan to extend the mold’s lifespan and ensure continuous production.
By comprehensively considering these factors, designers can develop reliable design solutions for blow molding molds for stacking buckets, achieving efficient, stable, and high-quality production.
Methods to improve the efficiency of blow molding process
The latest technologies and methods to improve the efficiency of blow molding processes include the following aspects:
Smart Control Systems: Implement advanced smart control systems that utilize sensors and automation to monitor key parameters in real-time during the blow molding process. This helps in adjusting production parameters promptly, enhancing production stability and consistency.
Optimized Mold Design: Utilize advanced mold design and manufacturing technologies, optimizing aerodynamics to improve the flow of plastic within the mold. This reduces energy consumption and enhances production efficiency.
Energy-Efficient Equipment: Upgrade and adopt energy-efficient blow molding equipment, including efficient heating and cooling systems, to reduce energy consumption and improve production efficiency.
Multi-Layer Co-Extrusion Technology: Introduce multi-layer co-extrusion technology in blow molding to simultaneously produce products with multiple layers. This enhances product performance, reduces production steps, and thus improves efficiency.
Material Innovations: Continuously research and adopt new plastic materials with better flowability, plasticity, and molding performance to improve production efficiency and product quality.
Real-time Data Analysis: Utilize big data and real-time data analysis technologies to monitor and analyze data during the production process. This helps identify potential issues and make timely adjustments to improve production efficiency.
Online Quality Monitoring:
Implement online quality monitoring systems using visual inspection and sensor technologies to monitor products in real-time, ensuring they meet quality standards and reducing defect rates.
Training and Skill Enhancement: Improve the training of operators to proficiently use new equipment and technologies, maximizing the efficiency of the equipment.
Automation of Production Lines: Introduce automated production lines that facilitate a fully automated process from raw material feeding, heating, molding, to cooling and demolding, enhancing production efficiency.
Green Production Philosophy: Promote a green production approach in blow molding, minimizing environmental impact and improving resource utilization efficiency.
The application of these technologies and methods can effectively enhance the efficiency of blow molding processes, reduce costs, improve product quality, and drive the blow molding industry towards more sustainable and advanced practices.
Contact Our Experts
TONGDA Clients
Successfully supplied Jerrycan blow molding machine lines to many countries around the world
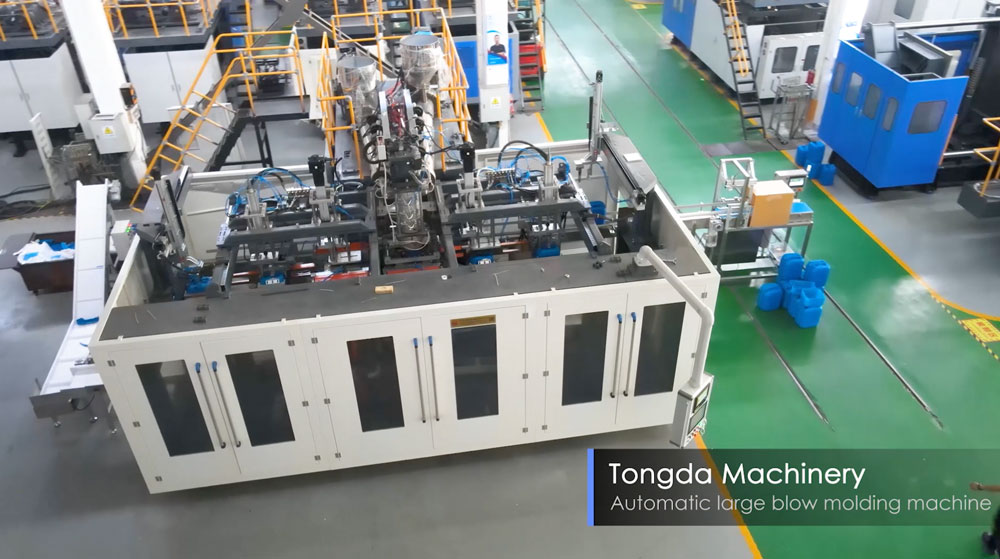
- Client Location: Mexico
- Model: HSII-30L
- Output: 120pcs/hr
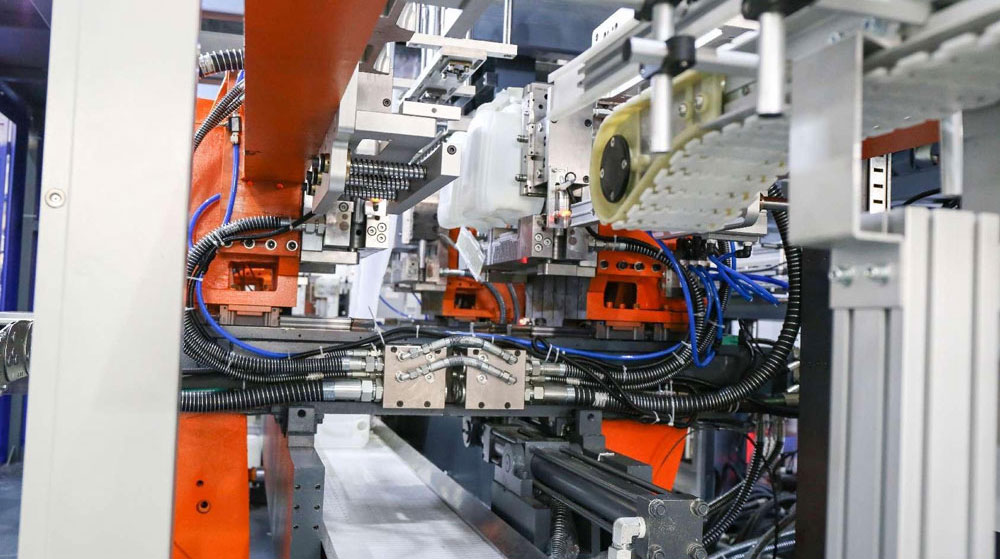
- Client Location: Ukraine
- Model: HSII-20L-2
- Output: 400pcs/hr
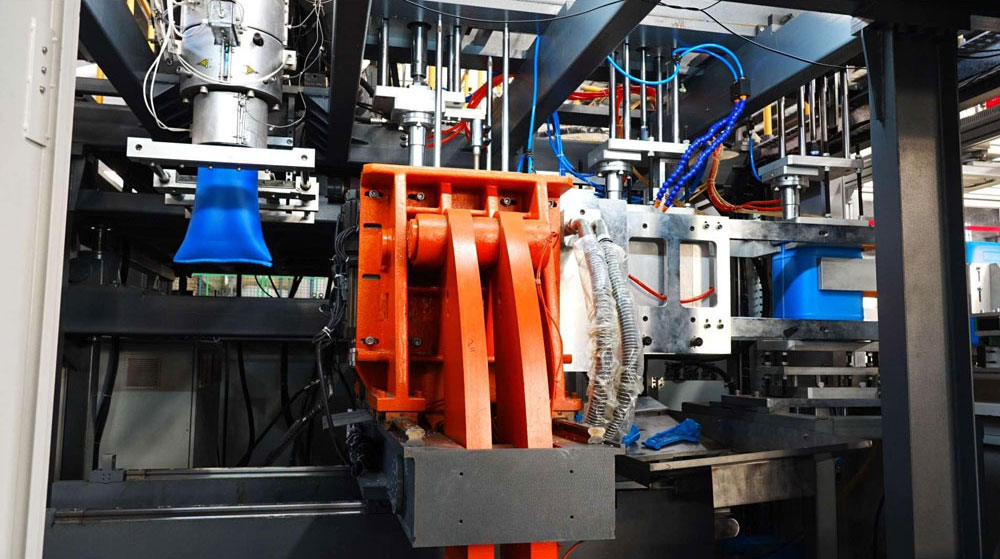
- Client Location: The Philippines
- Model: HS-30L/1
- Output: 60pcs/hr
Trusted By
Successfully supplied Jerrycan blow molding machine lines to many countries around the world
