The principle and classification of blow molding machine
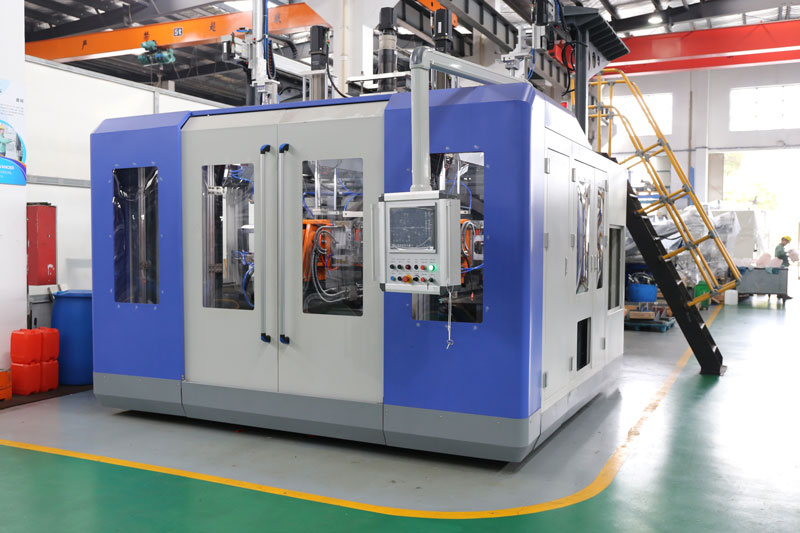
After the blow molding machine sprays the liquid plastic, the wind is blown out by the machine, and the plastic body is blown to a cavity of a certain shape to make a product. The plastic is melted and quantitatively extruded in a screw extruder, and then formed through a dough film, and then cooled by a wind ring, and then pulled by a tractor at a certain speed, and the winder winds it into a roll. Extrusion Blow Molding of thermoplastic pellets (or powder), after plasticizing through an extruder, through a specific die, to prepare a hot-melt tubular parison, which is then blow molded. Injection Blow Molding uses a split mold to inject a parison onto a mandrel. After the parison is properly cooled (to solidify the surface of the parison, the mandrel is not broken or deformed when moving the mandrel) Together with the parison, it is sent to the blow mold, the blow mold is closed, the compressed air is introduced through the mandrel, the parison is inflated to form the desired product, and the product is taken out after cooling and setting. Stretch blow molding allows the parison to be stretched and formed in a specific temperature range. At the same time of molding, large molecules are aligned and fixed in the wall of the product, thereby greatly improving the performance of the plastic container. A method in which a bottomed parison heated at a suitable temperature below the melting point is placed in a mold, and the light is axially stretched by a stretching rod, and then blown immediately. Multi-layer blow molding uses a multi-layer composite parison to prepare a multilayer container by a blow molding process. Through the reasonable matching of various plastic layers, the effective complementarity of the properties of the various layers of plastics is achieved, thereby overcoming some inherent disadvantages of single-layer plastic containers. It should be noted that within the two-plate injection molding machine, sufficient plastic raw materials should be maintained. Moreover, different raw materials should be dried to different degrees according to the needs, which also allows us to meet the processing needs of the process. In general, the personnel who operate the equipment need to be trained. If it is a novice, try to have a staff member to guide.