Exclusion equipment mold closing and blowing mold expansion instructions
TDB two-tie rod machine mold expansion inspection (25, 50/80/120/160/250 can be referred to the same reason)
During the initial on-site debugging, mold opening and closing may cause mold expansion. First observe the phenomenon:
1:Check the oil circuit to see if the oil drain pipe is not connected to the oil tank.
Check the mold closing proximity switch.
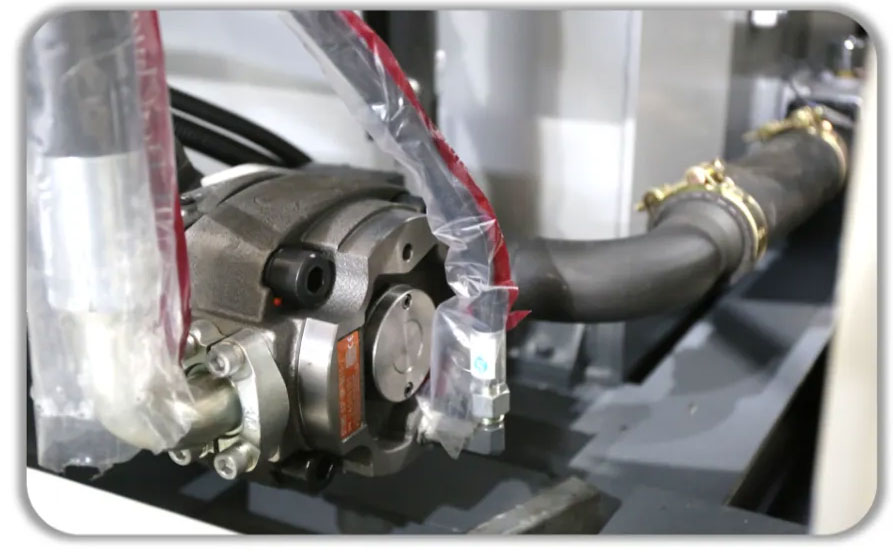
2:Check whether the mold clamping oil pressure can normally establish a pressure of 12MPa. If the pressure is abnormal, there is a problem with the parameter setting, and the pressure of 500-999 needs to be readjusted.
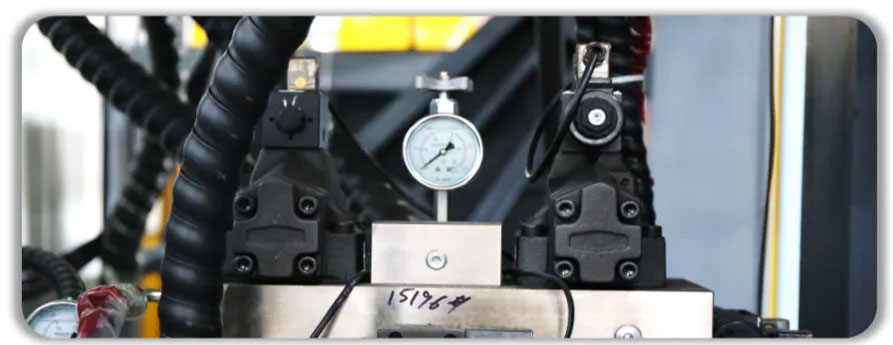
3:If the pressure is normal and the product has overflow and mold expansion, it is necessary to check the parallelism of the template and whether the assembly is correct.
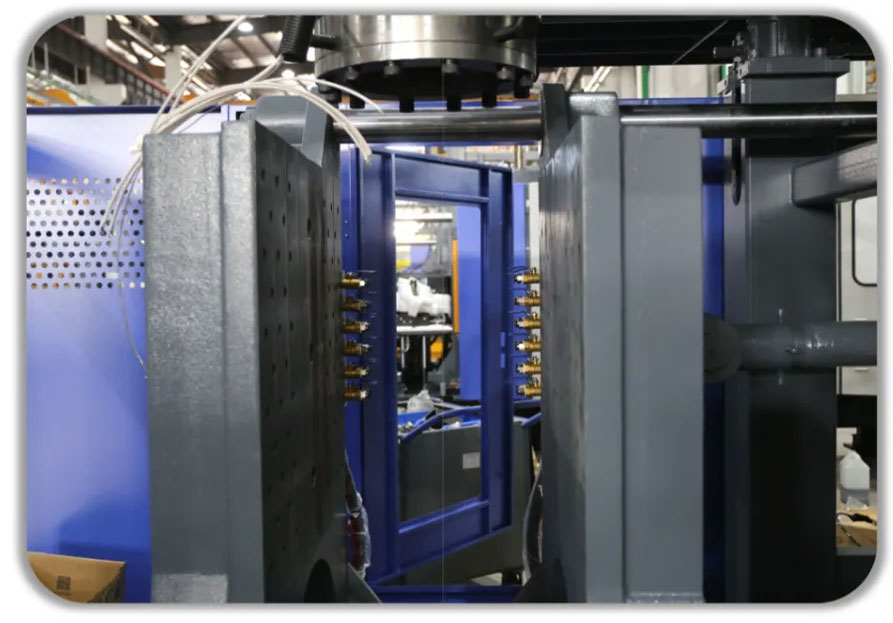
4:If the pressure continues to drop after the clamping time or the mold cavity pressure drops by more than 1.5MPa within 1 minute, this is also considered mold expansion.
- At this time, it is necessary to check whether the valve light ① installed horizontally on the rear side of the valve plate is closed during the tightening and pressure-maintaining stage, and check whether the hydraulic valve model is DSG-01-2B2-50T203.
- If the model and process status are correct, you can replace the new valve or the valve ① on the normally operating equipment to determine whether the pressure release is caused by the failure of this valve.
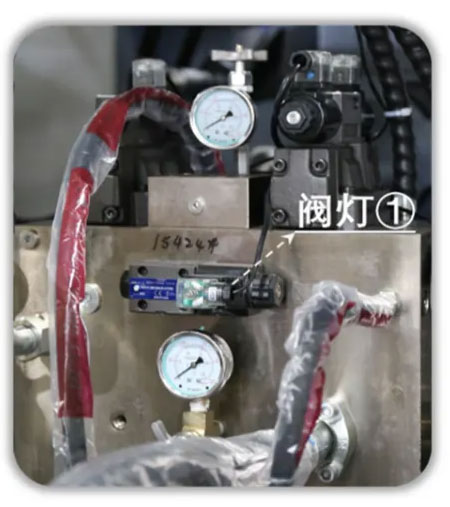
5:Replacing the cover
After checking and eliminating valve ①, unscrew the hexagon socket plug on the back side of cover plate ④, remove the damping screw plug inside, and then screw on the hexagon socket plug to observe whether the mold expansion phenomenon is improved. If not, replace the cover plate for testing.
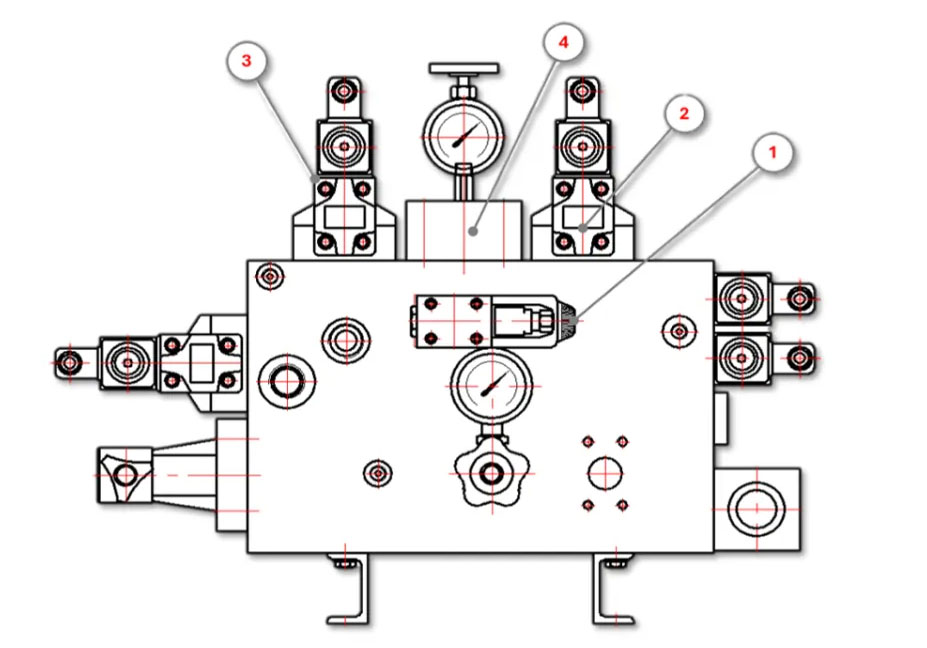
6:Replace ②③ hydraulic valves one by one to eliminate the quality problem of the hydraulic valve itself
7:Check for problems with components under the cover
Remove the cover plate and the entire set of plug-ins under the cover plate, and check the state of the sealing ring to see if there is any defect, crack or damage.
Check whether there is any burr or scratch on the processing surface of the valve plate plug-in installation hole. If there is any damage, it needs to be replaced in time.
8:Check the cylinder
If no abnormality is found in the above inspection, a set of high-pressure ball valve and pressure gauge should be connected in series between the clamping pipe of the rear end cover of the clamping cylinder (the pressure gauge should be located before the cylinder and the ball valve). Manually close the high-pressure ball valve from the start to the end of the tightening process and observe the pressure gauge value. If the pressure drops, it means that there is leakage in the cylinder and the cylinder needs to be checked and replaced.
If no abnormality is found in the above inspection, a set of high-pressure ball valve and pressure gauge should be connected in series between the clamping pipe of the rear end cover of the clamping cylinder (the pressure gauge should be located before the cylinder and the ball valve). Manually close the high-pressure ball valve from the start to the end of the tightening process and observe the pressure gauge value. If the pressure drops, it means that there is leakage in the cylinder and the cylinder needs to be checked and replaced.
a) Refer to the above steps 1-3 to check and replace the mold closing valve in the right figure ①,
verify the valve status.
b) If the mold expansion phenomenon is not eliminated, consider checking the installation of the plate-type hydraulic control one-way valve ② and consider replacing it, and verify the valve status.
c) Finally, perform the above step 8 to check the cylinder status.
b) If the mold expansion phenomenon is not eliminated, consider checking the installation of the plate-type hydraulic control one-way valve ② and consider replacing it, and verify the valve status.
c) Finally, perform the above step 8 to check the cylinder status.
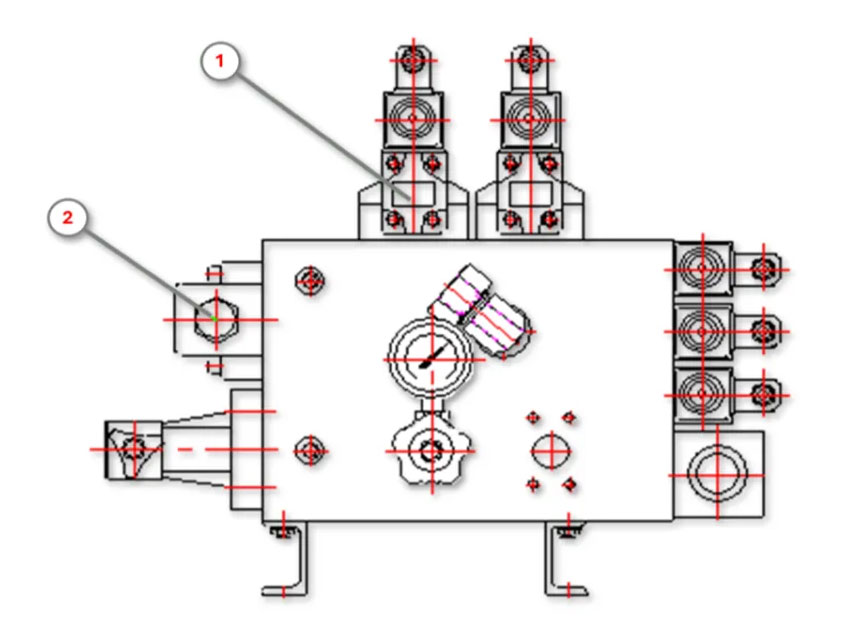
TDW rodless machine expansion mold inspection
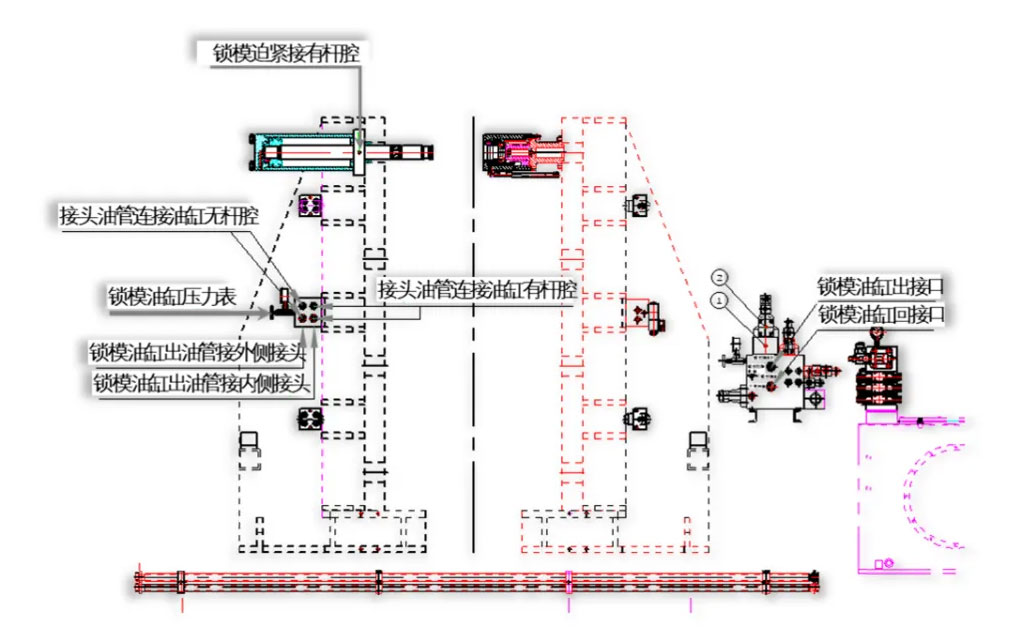
1:Check the oil circuit
The clamping oil circuit is connected to the steel pipe from the return interface of the clamping oil cylinder of the main valve plate, and then transported to the bottom of the oil distributor block of the front template, and connected to the inner joint of the oil distributor block according to the diagram. At this point, the clamping oil circuit is divided into four parts and finally connected to the rod chamber of the clamping oil cylinder.
The secondary oil circuit is unique and cannot be connected incorrectly as shown in the figure.
2:Check system oil pressure
Check whether the system oil pressure can normally establish the 12MPa test pressure. If the pressure is abnormal, there is a problem with the parameter setting, and the pressure corresponding to 500-999 needs to be readjusted.
Check whether the system oil pressure can normally establish the 12MPa test pressure. If the pressure is abnormal, there is a problem with the parameter setting, and the pressure corresponding to 500-999 needs to be readjusted.
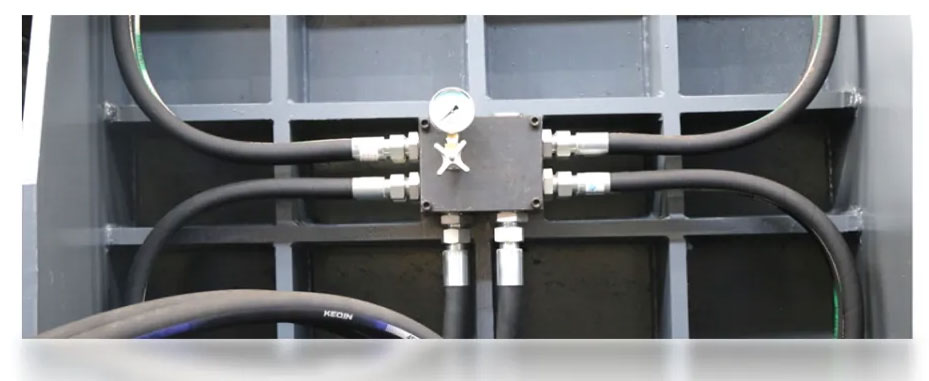
3: After checking that the oil circuit and pressure are correct according to the diagram
Observe the clamping cylinder pressure gauge on the front template. If the pressure gauge value drops during the pressure holding stage after the clamping is completed, it means that the clamping system has failed.
Further check the hydraulic valves ①②, models MPB-06-4, DG5V-8-6C-T, DG4V-3-6C, and ensure correct installation.
If there is no error in the inspection, replace ①MPB-06-4 superimposed hydraulic control check valve, confirm the status of the check valve, and solve the mold expansion, indicating that the check valve has failed.
If the mold expansion is not improved, replace ②DG5V-8-6C-T, DG4V-3-6C hydraulic reversing valve, and check the status of the reversing valve.
If it has not been improved, a high-pressure ball valve needs to be connected in series at the return oil pipe of the mold locking cylinder of the main valve plate. After the mold locking cylinder returns to its position for tightening, close the high-pressure ball valve before the tightening is completed, and observe whether the pressure holding pressure on the mold locking pressure gauge on the front template oil separator block is relieved. If it is relieved, it means that the pressure relief occurs from the oil separator block to the cylinder section, so replace the oil separator block first.
Verify whether the oil separator block defect cracks relieve pressure. If the status is not relieved, it means that there is an internal leakage and pressure loss in the mold locking cylinder. At this time, find the internal leakage cylinder and replace it.
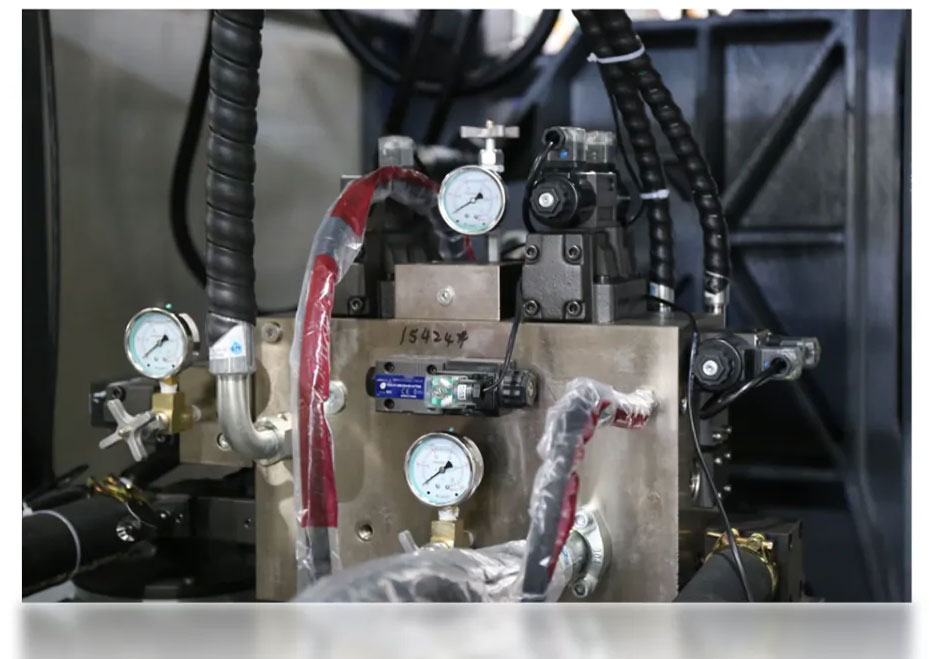
4: If the clamping oil circuit maintains pressure normally, it is necessary to check whether the valve plate has defects such as sand holes and air holes that cause pressure leakage.
Recent News
Blow Molding Machines for Sale
16 8 月, 2024
What is the best material for blow molding?
9 8 月, 2024
The solution to the shrinkage defect of the mold
8 8 月, 2024